Unraveling the Secret of Porosity in Welding: Tips for Lessening Issues and Optimizing Quality
In the complex globe of welding, porosity continues to be a persistent obstacle that can considerably influence the high quality and honesty of bonded joints. As we dig right into the midsts of porosity in welding, discovering the secrets to its prevention and control will certainly be vital for experts seeking to understand the art of premium weldments.
Recognizing Porosity in Welding
Porosity in welding, an usual problem encountered by welders, refers to the visibility of gas pockets or voids in the bonded material, which can jeopardize the stability and top quality of the weld. These gas pockets are usually entraped during the welding procedure because of different variables such as inappropriate shielding gas, polluted base materials, or inaccurate welding parameters. The formation of porosity can compromise the weld, making it at risk to splitting and corrosion, eventually leading to architectural failings.
Recognizing the root creates of porosity is crucial for welders to effectively stop its event. By acknowledging the importance of preserving proper gas shielding, ensuring the tidiness of base materials, and optimizing welding settings, welders can substantially minimize the chance of porosity development. Furthermore, using methods like pre-heating the base product, using correct welding strategies, and carrying out comprehensive evaluations post-welding can further aid in decreasing porosity issues. In general, a comprehensive understanding of porosity in welding is necessary for welders to generate top quality and resilient welds.

Usual Reasons For Porosity
When inspecting welding processes for potential high quality problems, comprehending the typical reasons for porosity is vital for preserving weld integrity and avoiding structural failings. Porosity, defined by the visibility of cavities or gaps in the weld metal, can considerably compromise the mechanical homes of a bonded joint. One usual reason for porosity is inappropriate shielding gas insurance coverage. Inadequate securing gas flow prices or incorrect gas mixtures can result in climatic contamination, causing porosity formation.
One more widespread reason for porosity is the visibility of dampness and contaminants on the surface of the base steel or filler product. When welding products are not appropriately cleaned or are subjected to high degrees of humidity, the vaporization of these impurities during welding can develop spaces within the weld bead. Furthermore, welding at improper specifications, such as exceedingly high traveling speeds or currents, can create extreme turbulence in the weld swimming pool, capturing gases and causing porosity. By attending to these typical reasons with correct gas protecting, product prep work, and adherence to optimal welding specifications, welders can minimize porosity and see here improve the quality of their welds.
Methods for Porosity Prevention
Implementing efficient preventative measures is important in lessening the event of porosity in welding procedures. One method for porosity prevention is guaranteeing proper cleaning of the base steel before welding. Pollutants such as oil, grease, corrosion, and paint can lead to porosity, so complete cleaning using ideal solvents or mechanical methods is vital.

Another key safety net is the choice of the right welding consumables. Utilizing top notch filler products and protecting gases that appropriate for the base steel and welding procedure can dramatically reduce the danger of porosity. In addition, maintaining correct welding parameters, such as voltage, existing, travel rate, and gas circulation price, is essential for porosity avoidance. Drifting from the advised settings can cause inappropriate gas coverage and inadequate blend, leading to porosity.
In addition, using proper welding strategies, such as preserving a regular traveling speed, electrode angle, and arc length, can help stop porosity (What is Porosity). Ample training of welders to guarantee they comply with finest practices and quality assurance treatments is also crucial in minimizing porosity issues in welding
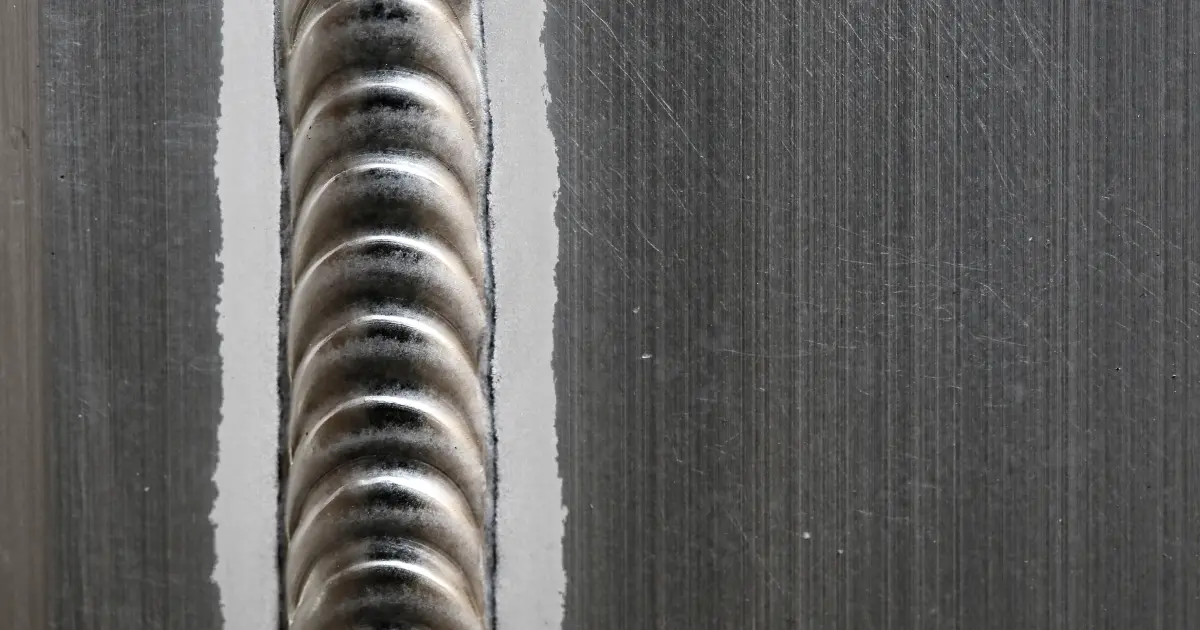
Finest Practices for Top Quality Welds
One secret practice is preserving correct cleanliness in the welding location. Thoroughly cleaning up the work surface and surrounding area prior to welding can help alleviate these issues.
An additional best webpage method is to carefully choose the ideal welding parameters for the certain products being joined. This includes establishing the appropriate voltage, existing, travel speed, and securing gas circulation rate. Appropriate criterion option guarantees ideal weld infiltration, fusion, and general top quality. Using top quality welding consumables, such as electrodes and filler steels, can dramatically influence the last weld quality. Investing in premium consumables can cause more powerful, extra sturdy welds with less problems. By adhering to these finest methods, welders can constantly create high-grade welds that fulfill sector criteria and surpass client expectations.
Value of Porosity Control
Porosity control plays a vital function in guaranteeing the integrity and top quality of welding joints. Porosity, defined by the presence of cavities or voids within the weld steel, can substantially compromise the mechanical residential properties and structural integrity of the weld. Too much porosity compromises the weld, making it more prone to splitting, rust, and overall failing under operational lots.
Reliable porosity control is vital for keeping the desired mechanical buildings, such as strength, ductility, and strength, of the bonded joint. What is Porosity. By minimizing porosity, welders can improve the total quality and dependability of the weld, making certain that it meets the performance needs of the desired application
Additionally, porosity control is vital for accomplishing the preferred visual appearance of the weld. Excessive porosity not only deteriorates the weld but also diminishes its aesthetic allure, which can be vital in sectors where aesthetic useful content appeals are essential. Proper porosity control techniques, such as utilizing the appropriate securing gas, regulating the welding criteria, and ensuring proper cleanliness of the base products, are important for generating high-quality welds with minimal issues.

Conclusion
In conclusion, porosity in welding is a common issue that can endanger the high quality of the weld. It is necessary to manage porosity in welding to guarantee the integrity and toughness of the last product.